De-Globalisierung: Wie die Zeichen für eine europäische Solarindustrie stehen
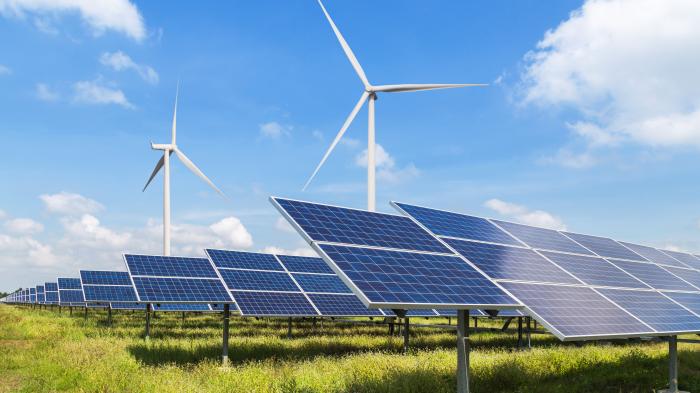
(Bild: Soonthorn Wongsaita/Shutterstock.com)
In unserer Serie zur De-Globalisierung beleuchten wir deutsche und europäische Abhängigkeiten von Rohstoffen und Lieferketten.
(This article is also available in English [1])
Sage und schreibe viermal so viel Sonnenstrom wie heute – das will die Bundesregierung bis 2030 erreichen. Doch woher sollen die ganzen Solarzellen kommen? Aus Deutschland wohl eher nicht. Dabei war die hiesige Industrie einmal weltweit führend. Anfang der 2010er-Jahre hat die damalige schwarz-gelbe Koalition sie durch extrem gekürzte Einspeisevergütungen ausgehungert. Heute gibt es hier nur noch ein Fünftel so viele Arbeitsplätze wie 2011. Der Markt ist mittlerweile fest in chinesischer Hand.
"Es ist naiv zu glauben, man müsste im Westen nur mit den Fingern schnipsen, und dann kommt für immer und ewig billige Ware aus China", sagt Gunter Erfurt, CEO des schweizerischen Solarmodulherstellers Meyer Burger. "Die chinesische Solarindustrie ist bereits extrem damit beschäftigt, den eigenen Markt zu bedienen. 50 Prozent der Produktion bleiben in diesem Jahr im Land."
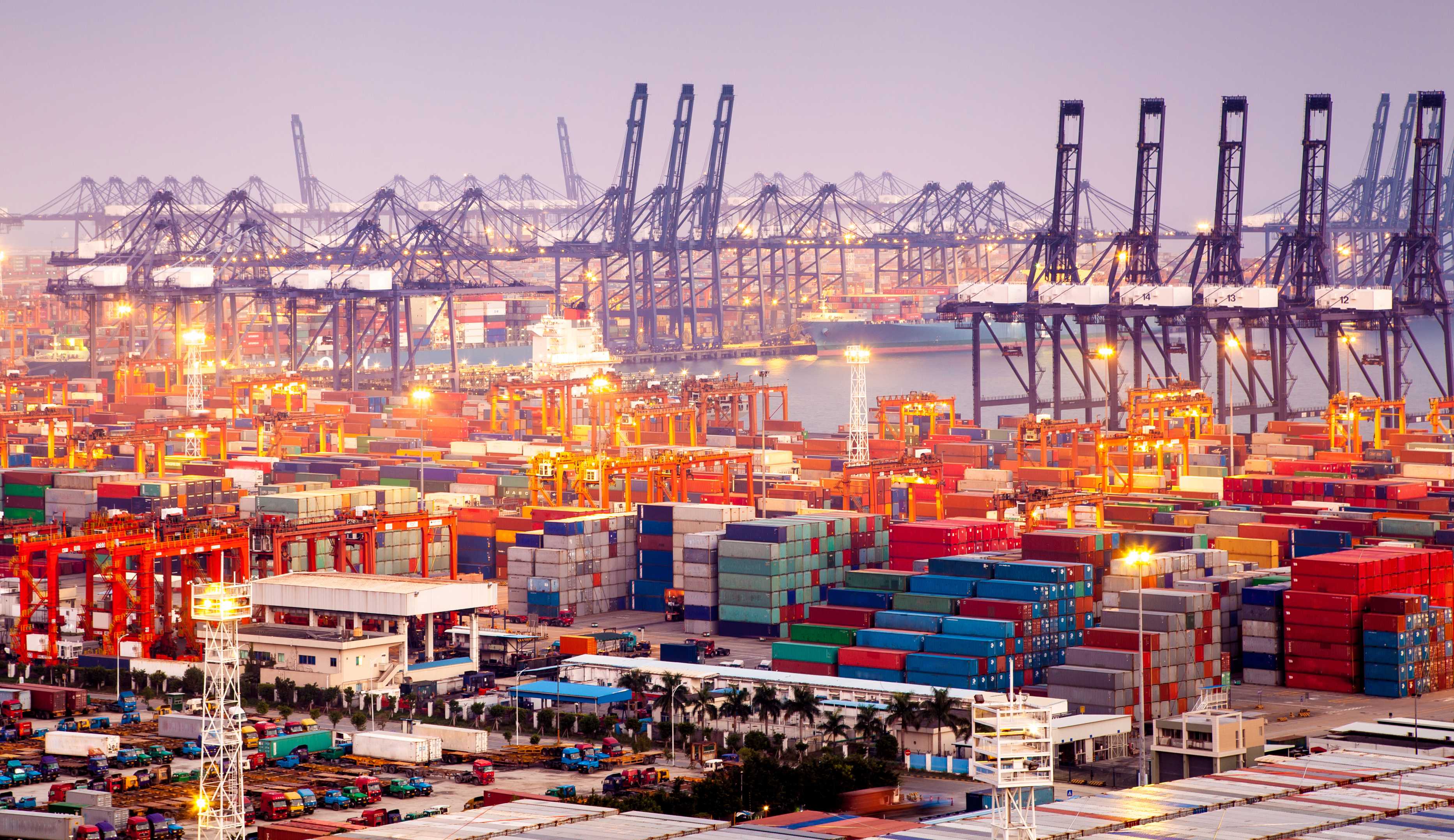
Shenzhen, Hafen von Yantian
(Bild: zhangyang13576997233 / Shutterstock.com)
Die vergangenen Monate haben schmerzlich gezeigt, dass die Abhängigkeit von Ressourcen einen hohen Preis hat. Doch lässt sich das Rad noch zurückdrehen? Werfen wir also einen Blick auf die Versorgungslage. Wie weit sich Europa mit strategisch wichtigen Rohstoffen selbst versorgen könnte und was das für die Industrie bedeutet, wollen wir mit einer Rohstoff-Artikelserie erkunden.
- De-Globalisierung – wie unabhängig kann Europa sein? [2]
- Kann Europa sich selbst mit Lithium versorgen? [3]
- Kann Europa sich selbst mit Seltenen Erden versorgen? [4]
- Kann Europa sich selbst mit Stahl und Aluminium versorgen? [5]
- Kann Europa sich selbst mit Kupfer versorgen? [6]
- Kann Europa sich selbst mit Kobalt versorgen? [7]
- Trotz neuer Batteriefabriken bleibt Abhängigkeit von China [8]
- Wie die Zeichen für eine europäische Solarindustrie stehen [9]
Seiner Beobachtung nach sei die Volksrepublik gerade dabei, einen "strategischen Zukunftsmarkt" zu kaufen. "Es wird trotz viel zu geringer Marge sehr viel investiert." Dazu komme: "In Europa müssen wir als europäisches Unternehmen, das in Europa produziert, Zölle für alle Komponenten zahlen, die wegen fehlender Lieferanten nicht aus der EU kommen. China hingegen darf komplett barrierefrei importieren. Das ist kein fairer Wettbewerb."
Solarindustrie: die Lieferketten im Detail
Wie kann Europa dieser gefährlichen Abhängigkeit entkommen? Die schlechte Nachricht: Die Lieferketten sind lang und kompliziert – und immer nur so stark wie ihr schwächstes Glied. Die gute: Sie haben bereits einige ziemlich starke Glieder.
Beginnen wir mit dem Ausgangsmaterial Silizium. Es ist als Bestandteil von Quarzsand praktisch überall verfügbar, muss aber zu Polysilizium aufbereitet werden. Zu den Marktführern zählt die Wacker Chemie AG mit Sitz in München. Gemeinsam mit Herstellern in Norwegen ließe sich in Europa jährlich genug Polysilizium für 20 bis 25 Gigawatt Photovoltaik-Leistung herstellen, schätzt Experte Jochen Rentsch vom Fraunhofer-Institut für Solare Energiesysteme (ISE) in Freiburg. Das würde immerhin für die deutschen Ausbauziele reichen.
Aus dem Polysilizium werden im nächsten Schritt "Ingots" erzeugt – Blöcke oder Zylinder, aus denen dann dünne Wafer gesägt werden. Hier ist Europa besonders blank. "96 Prozent der Ingots und Wafer kommen aus China", sagt Rentsch. "Selbst die Ausrüster dafür sind aus Europa verschwunden." Nicht viel besser sieht es bei der Zellproduktion aus – also dem Dotieren und Beschichten der Wafer.
Bleibt noch der Zusammenbau der Zellen zu montagefertigen Modulen. "In Europa gibt es dafür insgesamt nur eine Fertigungskapazität von acht Gigawatt pro Jahr, und die ist auf viele kleine Fertigungskapazitäten verteilt", sagt Rentsch. Das reicht nicht einmal für die deutschen Ausbaupläne.
Asiatische Produktion auf europäischem Know-how
Eine besondere Ironie der Geschichte: Ein großer Teil der asiatischen Produktion beruht auf europäischen Maschinen und Know-how, etwa auf Drahtsägen zum Zerteilen der Ingots. Wie konnte ausgerechnet dieser Teil der Wertschöpfungskette nun auch noch aus Europa verschwinden?
"Wir haben in den 2000er-Jahren eine Drahtsäge entwickelt, die eine Million Franken gekostet hat", erklärt Meyer-Burger-Chef Erfurt. "Später haben wir eine verbesserte Säge mit achtfacher Kapazität für nur noch 400.000 Franken verkaufen können. Wir haben also die Vervielfachung der Produktivität ermöglicht, bekamen das aber nicht entsprechend bezahlt. So wurden wir Opfer unseres eigenen technologischen Erfolgs."

(Bild: Quelle: Fraunhofer-Institut für Solare Energiesysteme (ISE), Aktuelle Fakten zur Photovoltaik in Deutschland [17], Stand: August 2022 )
Die Ursache für den Niedergang hiesiger Solarhersteller sieht er auch, aber nicht nur im politischen Versagen. "Wir Ausrüster hatten ebenfalls unseren Anteil daran. Wir haben zuerst die deutschen Unternehmen ausgerüstet und dann die Chinesen. Was dabei herauskam, war immer das gleiche Solarmodul als Produkt. Das macht es schwierig für den Wettbewerb." Meyer Burger hat daraus die Konsequenz gezogen und verkauft seine Anlagen nicht mehr an Dritte, sondern nutzt sie ausschließlich selbst, um Zellen und Module herzustellen. Das Know-how soll auf diese Weise nicht mehr nach außen fließen.
Neues Leben im "Solar Valley"
Zu besichtigen ist das Ergebnis dieser Strategie an einem symbolträchtigen Ort: dem "Solar Valley", einem unglamourösen Industriegebiet bei Bitterfeld-Wolfen. Hier schlug früher das Herz der deutschen Photovoltaikbranche, geprägt durch den damaligen Weltmarktführer Q-Cells. Letztes Jahr bezog Meyer Burger hier die leer stehende, 27.000 Quadratmeter große Halle des 2012 pleite gegangenen Solarproduzenten Sovello. Darin entsteht die einzige Zellfertigung Europas. Sie soll zur Keimzelle einer Wiedergeburt der deutschen Solarindustrie werden. Die ersten Zellen laufen bereits vom Band, daneben werden weitere Produktionslinien installiert.
Am Anfang der Produktion stehen millimeterdünne, zerbrechliche Silizium-Wafer. Wenn sie ankommen, haben sie bereits eine Weltreise hinter sich. Der Ausgangsstoff Polysilizium komme zwar "zu einhundert Prozent" aus Europa und den USA, betont Gunter Erfurt. Doch um ihn zu Ingots und Wafern weiterzuverarbeiten, muss er nach China. "Es geht noch nicht anders", bedauert Erfurt. Um sich unabhängiger zu machen, hat Meyer Burger kürzlich einen Liefervertrag mit Norwegian Crystals abgeschlossen, einen der beiden letzten europäischen Wafer-Produzenten. Aber das deckt nur einen Teil des Bedarfs.

(Bild: Meyer Burger)
Prozessoptimierung bei den Wafern
Mitarbeiterinnen und Mitarbeiter legen die Wafer von Hand in ein Tragegestell ein, das an einen CD-Ständer aus den 90ern erinnert. Alle weiteren Schritte geschehen automatisch. Sirrende Förderbänder und zischende Sauggreifer, abgeschirmt durch Glaskästen, befördern die Wafer durch chemische Bäder, Beschichtungskammern und Siebdruckanlagen.
"Wir haben die Zahl der Prozessschritte von mehr als zehn auf vier reduziert", sagt Fertigungsleiter Jochen Fritsche: Chemische Vorbehandlung, Passivierung, Beschichtung mit einer leitfähigen Oberfläche, Aufdrucken von silbernen Leiterbahnen. Dabei wechseln die Wafer ihre Farbe von metallisch-glänzend über silbrig-matt bis hin zum typisch schimmernden Dunkelblau.
Vieles bei der Prozessoptimierung ist Feintuning: Zur Beschichtung etwa liegen die Wafer nur ganz am Rand auf einem Transportrahmen auf. So können Ober- und Unterseite gleichzeitig behandelt werden. Wieder ein Arbeitsschritt gespart.
Eine weitere Verbesserung: "An keiner Stelle des Prozesses werden die Zellen mehr als 300 Grad warm – und auch das nur für wenige Minuten", sagt Fritsche. Bei herkömmlichen Verfahren herrschten hingegen für mehrere Stunden Temperaturen von mehr als 1.000 Grad. Entsprechend niedriger fallen Energieverbrauch und Ausschuss aus, entsprechend kürzer sind die Aufheiz- und Abkühlphasen.
Das eigentliche Geheimnis liegt in der Passivierung. Sie soll Ladungsträgerverluste an der Oberfläche reduzieren. Bei "Heterojunction"-Zellen, wird dazu beidseitig eine dünne Schicht amorphen Siliziums aufgebracht. Dies soll nicht nur Spannung und Strom erhöhen, sondern auch die Umwandlung von diffusem Licht. Zudem sind die Module bifazial, können also Licht von beiden Seiten nutzen. Das Ergebnis ist laut Meyer Burger ein Wirkungsgrad von bis zu 25 Prozent auf Zellebene, rund ein Viertel mehr als herkömmliche Silizium-Rückkontaktzellen. Die Heterojunction-Zellen sollen zudem langlebiger und weniger temperaturempfindlich sein. Auf Module mit Glasrückseite gibt Meyer Burger eine Garantie von 30 Jahren.
Mitarbeitende von früher kommen zurück
Hand anlegen müssen Menschen erst wieder, um die fertigen Zellen für den Weitertransport ins sächsische Freiberg einzupacken. Dort werden sie dann zu Modulen verbaut – ebenfalls in einer reaktivierten Solarfabrik. Sie gehörte zum untergegangenen Solarworld-Konzern, stand jahrelang still, war aber noch mit gut gepflegten Maschinen von Meyer Burger bestückt. Auch viele der Mitarbeitenden haben schon während der ersten Welle in der Solarindustrie gearbeitet – und seien nun "mit großer Begeisterung zurückgekommen", so Fritsche.
In der ersten Aufbaustufe will Meyer Burger im Solar Valley jährlich Zellen mit insgesamt 400 Megawatt produzieren. Bis 2023 sollen es 1,2 Gigawatt werden. Das entspricht knapp einem Viertel des gesamten deutschen Zubaus von 2021 – ein großer Schritt gegenüber dem Status quo, aber ohne Importe wird es wohl auch künftig nicht gehen.
Für 2024 ist der Bau einer weiteren Gigawatt-Zellfabrik geplant, idealerweise ebenfalls im Solar Valley. "Für die Zellfertigung braucht man eine gewisse Dichte an technologischem Know-how", sagt Produktionsleiter Fritsche. Deshalb solle die Zellfertigung an einem Standort konzentriert bleiben. "Die Modulfabriken werden hingegen dezentral aufgebaut, nahe an den entsprechenden Märkten" – schon wegen der höheren Transportkosten der voluminösen Module. Die zweite Modulfabrik von Meyer Burger entsteht derzeit in Arizona.
Nachhaltiger Aufschwung oder Strohfeuer?
Bei den Zellen und Modulen tut sich also etwas. Doch was ist mit der Wafer-Produktion? Hier setzt das Freiburger Start-up NexWafe an, eine Ausgründung des Fraunhofer ISE. Es will Silizium direkt zu Wafern verarbeiten, statt es erst aufzuschmelzen, erstarren zu lassen und zu zersägen. Dazu wird es verdampft und setzt sich dann als hauchdünne Schicht auf einem wiederwendbaren Saat-Wafer ab. Das erspart nicht nur die Drahtsäge, sondern senkt auch den Materialverbrauch. Laut NexWafe verursacht das Verfahren 30 Prozent weniger Kosten und 70 Prozent weniger CO2-Emissionen als eine herkömmliche Wafer-Produktion.
Bewahrheiten sich die Ankündigungen in der Praxis, habe das Verfahren das Potenzial, "die klassische Wafer-Produktion im Laufe der Zeit abzulösen", urteilt das Fachmagazin Photon. Bisher existiert allerdings erst eine Pilotlinie in Freiburg. Die Serienproduktion wurde immer wieder verschoben. Nun soll sie 2024 beginnen. Geplanter Standort ist – Überraschung! – das Solar Valley.
Solarindustrie: Wie es künftig aussieht
"Wichtig ist eine gesicherte Marktperspektive", meint Fraunhofer-Forscher Rentsch. Angesichts der ehrgeizigen Ausbauziele sei die Lage heute deshalb eine ganz andere als vor zehn Jahren. "Damals gab es Wachstum nur mit entsprechenden Anreizen. Heute sind die Gestehungskosten so niedrig, dass es sich von alleine trägt. Deshalb kann man guter Hoffnung sein, dass die Branche nicht plötzlich wieder einbricht." Wettbewerbsfähig seien europäische Fabrikation jedenfalls: "Früher hieß es immer: In Asien gibt es niedrigere Lohnkosten. Aber das Argument zieht heute nicht mehr, weil die Fertigung hochautomatisiert ist. Und dazu kommen noch steigende Transportkosten."
Und was ist mit den Fachkräften? Für die Herstellung von Zellen und Modulen macht sich Rentsch wenig Sorgen: "Die Fachleute für Fabrikautomatisierung sind nicht so spezialisiert, dass sie nicht auch aus anderen Branchen kommen könnten" – etwa wenn Zulieferer für Verbrennungsmotoren ihre Portfolios wegen der zunehmenden Elektrifizierung ändern müssen.
Bei der Installation der fertigen Module sei die Lage allerdings etwas anders, so Rentsch: "Da fragt man sich schon, wie das vonstattengehen soll." Andererseits habe es schon vor zehn Jahren genug Handwerker gegeben, um immerhin sieben Gigawatt pro Jahr zu installieren. "Jeder Dachdecker war damals auch Solarteur. Das müsste wiederkommen."
Vieles spricht also dafür, dass die europäische Solarindustrie zu alter Stärke zurückfindet – vor allem die gewaltige Nachfrage. Doch ein Selbstläufer ist dies nicht angesichts der verwickelten internationalen Liefer- und Wettbewerbsbeziehungen.
Politische Instrumente, das zarte Pflänzchen zu hegen, gäbe es genug: Mit den Important Projects of Common European Interest und dem European Chips Act [18] leitet die EU Milliardensummen in die Wasserstoff- und Batteriezellforschung beziehungsweise in den Aufbau einer eigenen Chip-Industrie [19]. So etwas wünschen sich Vertreter der Solarindustrie auch für ihre Branche. Das Geld wäre, meint Gunter Erfurt, gut angelegt: "Für eine Produktionskapazität von 30 Gigawatt pro Jahr müsste man europaweit einmalig, quer durch die Wertschöpfungskette, etwa 10 bis 12 Milliarden Euro investieren. Das ist etwa halb so viel wie die jährlichen Kosten für den Import fossiler Energie aus Russland."
Auch die aktuelle Ausgabe der MIT Technology Review beschäftigt sich mit dem Thema Deglobalisierung. In verschiedenen Texten gehen wir der Frage nach, inwieweit es möglich ist, Prozesse der Deglobalisierung wieder zurückzudrehen. Das neue Heft ist seit dem 28.9. im heise shop bestellbar [20] und seit dem 29.9. im Handel erhältlich.
(jle [22])
URL dieses Artikels:
https://www.heise.de/-7279541
Links in diesem Artikel:
[1] https://www.heise.de/hintergrund/De-globalisation-How-the-signs-stand-for-a-European-solar-industry-7283272.html
[2] https://www.heise.de/hintergrund/Neue-Serie-De-Globalisierung-Wie-unabhaengig-kann-Europa-sein-7251008.html
[3] https://www.heise.de/hintergrund/De-Globalisierung-Kann-Europa-sich-selbst-mit-Lithium-versorgen-7223228.html
[4] https://www.heise.de/hintergrund/De-Globalisierung-Kann-Europa-sich-selbst-mit-Seltenen-Erden-versorgen-7259585.html
[5] https://www.heise.de/hintergrund/De-Globalisierung-Kann-Europa-sich-selbst-mit-Stahl-und-Aluminium-versorgen-7243606.html
[6] https://www.heise.de/hintergrund/De-Globalisierung-Kann-Europa-sich-selbst-mit-Kupfer-versorgen-7261735.html
[7] https://www.heise.de/hintergrund/De-Globalisierung-Kann-Europa-sich-selbst-mit-Kobalt-versorgen-7269182.html
[8] https://www.heise.de/hintergrund/De-Globalisierung-Trotz-neuer-Batteriefabriken-bleibt-Abhaengigkeit-von-China-7260696.html
[9] https://www.heise.de/hintergrund/De-Globalisierung-Wie-die-Zeichen-fuer-eine-europaeische-Solarindustrie-stehen-7279541.html
[10] https://www.heise.de/select/tr/2022/7/2223507373444018741
[11] https://www.heise.de/select/tr/2022/7/2223507551085900156
[12] https://www.heise.de/select/tr/2022/7/2223511204162281198
[13] https://www.heise.de/select/tr/2022/7/2223511563977808397
[14] https://www.heise.de/select/tr/2022/7/2223508271525928736
[15] https://www.heise.de/select/tr/2022/7/2223511300301501427
[16] https://shop.heise.de/technology-review-07-2022/Print?wt_mc=intern.shop.shop.tr_2207.dos.textlink.textlink
[17] https://www.ise.fraunhofer.de/content/dam/ise/de/documents/publications/studies/aktuelle-fakten-zur-photovoltaik-in-deutschland.pdf
[18] https://www.heise.de/news/European-Chips-Act-Sofortmassnahmen-gegen-Lieferengpaesse-umstritten-6656561.html
[19] https://www.heise.de/select/tr/2022/7/2223507464597483104
[20] https://shop.heise.de/magazine/mit-technology-review/magazine/
[21] https://www.instagram.com/technologyreview_de/
[22] mailto:jle@heise.de
Copyright © 2022 Heise Medien